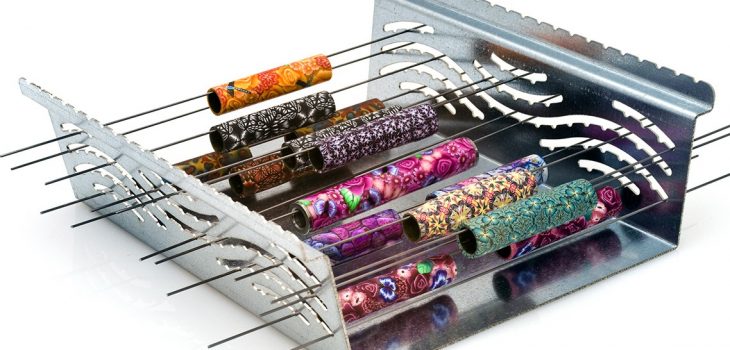
Polymer Clay Pen Blank Starter Guide
Handout: AAW Symposium 2016 Atlanta, GA. Connecting Polymer Clay to the Pen World
Instructor: Toni Street.
What is Polymer Clay:
Polymer Clay is a manufactured modeling compound that remains soft until cured in the oven. Polymer Clay is a combination of Polyvinyl Chloride (PVC), plasticizer and pigments. Different combinations of these substances give each brand of clay its distinct qualities. PC bakes at a low temperature between 230 degrees – 275 degrees Fahrenheit. PC is the most versatile and forgiving medium on the planet.
Different Brands:
There are several clay options available through craft stores and the internet, i.e. Michaels, Hobby Lobby, Polymer Clay Express.com and Munro Crafts.com to name a few.
They all have different benefits and limitations in regard to workability, strength flexibility and firmness.
All Clays have an indefinite shelf life if properly stored. However, the amount of time clay remains in the conditioned state depends on the firmness of the clay.
The following is a breakdown of the most common Polymer Clay types:
- Sculpey III: One of the first clays to be introduced. It is very soft and easy to condition. It bakes firm, but is not flexible and tends to be brittle after baking. I do NOT recommend this clay for pen turning.
- Premo by Sculpey: Very soft and pliable excellent range of 30 colors. When baked its flexible. It is known for being stickier than other brands and may need to be leached (pressed between paper) to remove excess oils. It is one of the brands I do recommend for pen turning.
- Fimo Classic: It’s the oldest and widely recognized Polymer Clays. It is one of the strongest and most resilient clays after baking. Offering an excellent degree of flexibility. Very stiff to condition. 24 colors. Can be used in pen turning.
- Fimo Soft: This is one of the easier clays to condition. Fimo Soft also offers the least amount of resistance or “blade drag” when slicing. It has good strength and flexibility after backing it is available in 50 colors. Can be used in pen turning.
- Kato: It can be stiff out of the package and takes longer to condition, but it offers excellent strength and flexibility after baking. It is available in 17 colors. It can be used in pen turning.
Work Surfaces/Tools:
A smooth ceramic tile is the best work and baking surface for polymer clay. I personally use a glass sheet, but this cannot go into the oven. Your work must be transferred to a ceramic surface.
Any gadget/tool can be of great use in polymer clay work, but they must be dedicated to the clay and never used in food preparation again. I also do not recommend eating near your workstation
Clay Conditioning and Handling:
Conditioning your clay is pretty self-explanatory. Even though you open up the package of clay and it is soft and pliable it stills needs to be conditioned. All Polymer Clay must be conditioned to restore the clay to a useable state. By conditioning the clay, you are softening up the clay, so that its particles are realigned. This is very important as this will give the clay maximum strength and the strongest adhesion.
- Wash hands to keep dirt and debris off the clay.
- Open the package, stand the brick of clay up on one end and use a blade to cut it into thick slices.
- Using an acrylic rod, thin the clay by rolling the rod over the clay. Keep doing this until the clay begins to thin out, by doing this you will minimize crumbling and shredding of the clay.
- Fold the clay in half and roll again.
- Now you are ready to place it through the pasta machine on the thickest setting. Roll the clay through the pasta machine.
- Change the pasta machine setting to medium, #3. DO NOT fold the clay in half, run the clay through the pasta machine again.
- Fold the clay in half and continue running it through the pasta machine on the #3 setting until the clay is soft and pliable. Look at your sheet of clay it should have a soft sheen and be free of air bubbles and surface imperfections.
Storing Your Clay:
Polymer clay begins curing at approximately 266 degrees Fahrenheit, so the location you choose to store your clay is very important. Make sure the clay is not exposed to heat or direct sunlight. Place it where the temperature is low, but not freezing!!
Raw clay may be wrapped with plastic wrap, covered with a sheet of plastic wrap, placed in a zip lock bag or in a plastic container, i.e. Tackle box. By doing this you will keep the clay clean from dust, hair and any debris. There is nothing worse than using the clay the next day only to slice through it and have cat, dog, etc. hair in the design!!
Baking/Curing your Polymer Clay:
Curing polymer clay transforms it from soft clay into a rigid plastic. Clay is cured by exposing it to temperatures ranging from 266 degrees Fahrenheit and up. Each brand has its own recommended time and temperature and these recommendations should be followed to the letter. To achieve the maximum strength, the recommended temperature must be reached.
It’s a good idea to use an oven thermometer and timer. With the thermometer you can keep an eye on the temperatures. Oven temperatures fluctuate and don’t always heat up at the temperature the oven is set to. When I bake my pieces in the oven I always leave the thermometer in, so I can check to make sure the temperature is holding steady, if not I can always increase or decrease it. ALWAYS pre-heat your oven to the desired temperature before placing your pen blanks in.
I do recommend buying a dedicated oven to cure your pen blanks in completely. Although Polymer Clay is labeled non-toxic, it is not to be used in conjunction with food items!! If you must use your home oven to cure your pen blanks use tin foil to tent over the pen blanks to keep the fumes inside and keep any residue from gassing onto the oven walls.
I suggest baking your pen blanks on a bead rack. The pen blankwill get cured from all sides and it’s easier to bake.
I recommend baking your pen blanks according to the manufactures directions on the clay that you choose to use.
Finishing:
Once your pen blanks have cooled down you are now ready to turn them. These directions are for finishing your pen blanks that have Millefiori designs on them. Place the pen blanks with the bushings on the mandrel for the kit the pen blanks are for. Make sure it’s on center. Very lightly sand using 800 and / or 1,000 grit sandpaper, I recommend Abranet. Without turning on your lathe sand the pen blank back and forth lightly to make it smooth, slowly turning the pen blank around. You want to be very careful not to sand the design off!! Once you have gone all the way around turn your lathe on and put some polish to clean the pen blankfrom any dust or clay particles. To apply polish put a little on a paper towel and go back and forth on the blank. Once its clean apply CA to the blank with the lathe spinning spray with accelerator. Once dry use sandpaper to smooth it out and then polish again. VOILA’ you are done!! Assemble your pen!
Resources:
Books:
- Pen and Pencil Projects a guide for woodturners~by Walter Hall
- The Art of Polymer Clay ~by Donna Kato
- The Polymer Clay Techniques Book ~ by Sue Heaser
- Polymer Clay for the first time ~ by Syndee Holt
- Creative ways with Polymer Clay ~ Dotty Mcillian