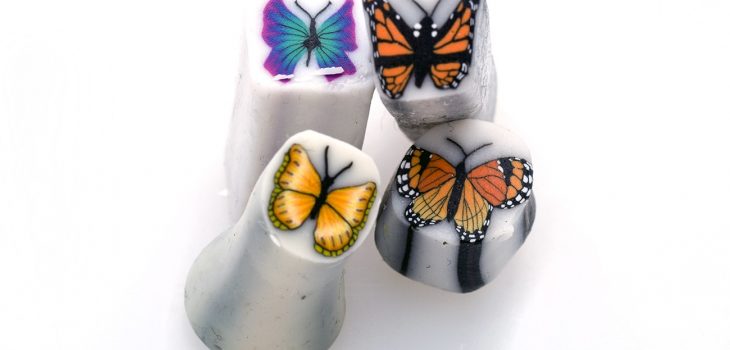
Cyanoacrylate ‘CA’ Treatment
Polymer clay itself does not really need a coating, however due to the construction of the pen blanks (pen tubes), and the harsh and often abusive environment that pens are subjected it is preferred to have a treatment coat over the pen blanks (pen tubes) to help bond everything together and add strength. The pen blanks on the inside provides structural support and the coating on the outside provides a skin like mesh that prevents the cane slides from sheering off and causing a disaster to happen.
In the polymer clay community a number of products are used such as Varathane. However in the pen community we have a few options. Namely CA and Casting.
-
What is CA
‘CA’ or more technically Cyanoacrylate glue is a class of fast acting adhesives. The chemical makeup is mostly Ethyl-2-Cyanoacrylate, however odorless is more of a special breed and for pen making more desirable.
-
How CA works
CA in its liquid form contains a ‘stabilizer’ which is a very mild acid. When the PH is shifted towards neutral polymerization occurs which sets the CA into the cured state. The more drastic change in PH the faster the polymerization, in a drastic form it can start fires by heat and speed generated.
If the CA comes in contact with an alkaline, i.e. some shop towels, baking soda, it will start smoking. Heat becomes a problem at this point and the cured CA will become brittle. Brittle coatings have no shock absorbing properties and they crack with easy.
One such problem has existed for many with a ‘shattered glass’ look. When I looked into this problem I noted two distinct groups: Those that crack quickly and those that crack over time. The group that cracks quickly is more related to the activator/accelerator, old glue or when the CA smokes. The group that cracks over time is more related to movement of the blank, wood grain moving, papermoisture content, shock that the pen undergoes (dropped, banged around, severe thermal changes).
- Group 1: Short term cracks: This is the common problem you see, you turn the pen blanks and in a few short hours the finish spiderwebs and cracks. This is caused for several reasons. The thickness of the glue is was to thick when applying and the inside near the clay is not fully ‘cured’ while the outside is hard and brittle. When the inside polymerizes it will cause a shift in the outter layer and that causes stress fractures in the CA and eventually it will crack, thus causing the shattered glass look.
- Group 2: Long term cracks: Same concept except the material moves over time. This is more of a problem with wood than polymer clay. Wood grain moves with moisture.
-
Accelerator
Some activator/accelerator contains nasty ingredients such as acetone. Acetone is a de-bonder and REMOVES CA. Spraying this on polished CA will deglaze it, meaning it will remove the shine and cause the CA to un-cure. Be very careful what is in your activator/accelerator, if unsure read the MSDS!
Acetone is a low cost cheap product that does cause CA to polymerlize however there are many bad effects that can happen. Brands that use acetone include but not limited to the following (ReadBAD to use, less than desirable):
- Stick-fast
- EZ-Bond
- Star Bond
- CA Plus
- Loctite 7452
- 2P-10
- Extreme Power (hobby lobby brand)
Two common products that stands out is Naptha and Heptane. Brands that does NOT use acetone include the following (Read GOOD to use):
- Bob Smith
- NCF Satellite City
- Titebond
- Zap
- Loctite 712
- Mercury
-
The case for Flex
CA with flex allows a higher quality standard, not only during production but in the pens life cycle. There is a clear rubber byproduct which will give CA a spring effect. It does not fully harden to a brittle state thus preventing cracks. If the material moves then the CA finish will move with it. I have taken pen blanks with CA on it, put it in my nova chuck and tightened the chuck and after removing the pen blanks you can see grooves carved into the CA. This is an extreme testing case in favor of using a flex CA but it also is worth noting that when a pen is dropped, banged, bent, sat on and the like it will bend with the abuse and absorb shock. This also helps protect the underlying blank material from some harm. If wood moves then the CA will move with it to some degree, some brands will just crack while the wood moves because they are very brittle when applied.
‘Flexible’ additives like PMMA (poly methyl methacrylate) reduces the brittle point and often found in products that need a light weight shatter resistant, impact force like Plexiglas, Lucite, Acrylite and Perspex. Other brands such as super-gold by BSI use other ingredients which works even better.
-
The case for odorless CA
CA when used has a harsh odor and over time many becomes sensitive to it, even develop non-allergenic asthma. This reaction is normal and causes nasty problems with very harmful effects. It causes reduced breathing, sensory irritation, asthma reactions, and flu like symptoms, dizziness, and headaches just to name a few. The solution to this case is twofold, a) Use of a respirator with a vapor fume rating, i.e. P100 cartridges along with better ventilation. And B) Switch to another type of glue, i.e. odorless. A respirator will stop vapors from being breathed but miss the contact problems associated with using CA. The sad fact is once you become sensitive there’s no going back, it’s best to treat your body right and not suffer.
-
Primer (Pre-base coat work)
Before we apply glue our surface *MUST* be dry, the least amount of moisture contained in the blank as possible. The PH also needs to be considered as alkaline really will mess things up bad. Products such as modpodge will retain moisture and will take WEEKS to fully dry. Adding a CA coat over top of this will result in failure. Our surface must be dust free, oil free, grease free and scratch free. The sanding direction should be end to end, bushing to bushing with the lathe turned OFF, with a very fine grit, 800-1500 grit range. Once the coating is complete it will magnify and amplify properties on the blank so any scratches and the like will stick out stronger than before.
Before we apply the first drop of CA I suggest using some type of paste wax and wax the bushings on the ends. This way the CA will stick less to the bushings and will be very easy to come off, also it gives us a visual reference point as to how thick the CA is when the lathe is running. With this method there is no need for special bushings like delrin (odorless CA will indeed bond delrin bushings and craft foam). CA is measured in centipoise, called CPS. CA glue runs from near 1 CPS (super-thin) to around 1,000 CPS (super-thick) The thin can soak into material before it starts to set while the thick provides barrier protection and adds bulk.
-
Applying the base coat
As with any paint job on a vehicle the base coat is the first filling over the base material. In our case we have a very rough surface and we need thin CA to cover that. We do NOT want the CA to bond instantly but instead soak into the material, all of those small crevices, gaps and the like, then and only then do we want it to cure. This practice, slow cure, is one of the keys to 3D effects with a CA finish.
Here at this stage you can apply as much CA as you need. Many seem to get hung up with the number of coats and they forget the most important thing is to build up the low areas. With the odorless CA that I use I can easily apply this in one pass because of the drastic increase in cure time.
-
Applying the filler coat
After our base coat is down we need to move to gap filling. All this does is uses a thicker CA and fills up any imperfections left behind. There will be low spots, gaps, cracks, crevices and non-round sections that must be dealt with at this stage.
5 COMMENTS
thank you
l use mineral oil as the first coat
Mineral oil can be used for some added effects. Also worth note mineral oil will slow the polymerization process.
However, the odorless CA has the same effects with out using mineral oil.
Hello,
Mineral oil is not needed if you are using odorless. The effects you have with mineral oil is already in the CA, that’s the benefit of using CA with known good additives. In BSI’s super-gold case the holographic effect is also in the CA due to the chemical that is used.
Awesome write up! You mentioned bad effects of acetone based accelerator, could you elaborate on that? Are there bad effects beyond the acetone dulling the finish?
Thank you!
Hello!
Acetone does cause CA to polymerize however it is way fast which causes excessive heat and the CA to be VERY brittle. Acetone is also cheap which is why many companies use it for CA accelerators.
A good test of this is to coat a pen blank with CA and acetone then abuse it, either something like throw it on a hard floor or put it in pliers and look at the results. What you are looking for are cracks and dents.
A good finish will DENT and not crack.